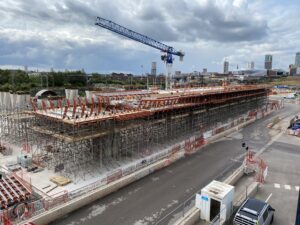
Versatile and connected equipment
To help support the construction of a structure of this size, Altrad RMDK had to specify several interconnected products, combining their Rapidshor falsework system with Alform aluminium beams and Superslim Soldier formwork beams to create the formwork cradles. Slimshor propping with clear span steel beams and further Alform decking beams were used to support the deck soffit over the “V” shaped void in the piers, with Megashor wailings to stabilise the side shutters.
A fully braced falsework system was the chosen method of support, with supports at 1.2-metre centres down the length of the viaduct. A fully braced method was required so that the structure would not move in any direction and was entirely restrained by its internal bracing. Altrad RMDK achieved the deck profile with a system of aluminium wailings & Superslim primary beams – which sat on the top of the falsework and incorporated a cantilevered support to the wings of the deck. Again, this ensured the structure was then all internally supported – mitigating the need for use of external props to the ground.
Due to the tight radius curves on the underside of the decks, a special formwork solution was designed to ensure the desired form and finish was met. Altrad RMDK worked closely with Cordek Ltd for this part of the project to precisely achieve the right shape and finish, devising a complete solution for the rounded corners, which proved to be rather complicated.
Maximum efficiency and safety
To ensure the project was a success, the formwork solution had to be as efficient as possible. The safe working load for the Rapidshor legs is 8 tonnes; and the engineering team took the design close to the limit at 7.85 tonnes. Doing this allowed the project to be completed efficiently and safely without compromising the foundations and preventing overloading.
To minimise the dangers that arise when working at height, the falsework solution was designed so that it could largely be constructed horizontally and connected before being craned into a vertical position. By erecting horizontally as opposed to vertically, it meant that the time working at height was greatly reduced, improving safety conditions on site.
Despite the large scale of the project, the innovative design of Altrad RMDK’s solution improved the sustainability of the project as it allowed the whole temporary works structure to be lifted away and then be used elsewhere on site, saving the customer time and money as the falsework and formwork did not need to be taken down and re-built.